How Control Instrumentation Enhances Process Accuracy and Plant Reliability
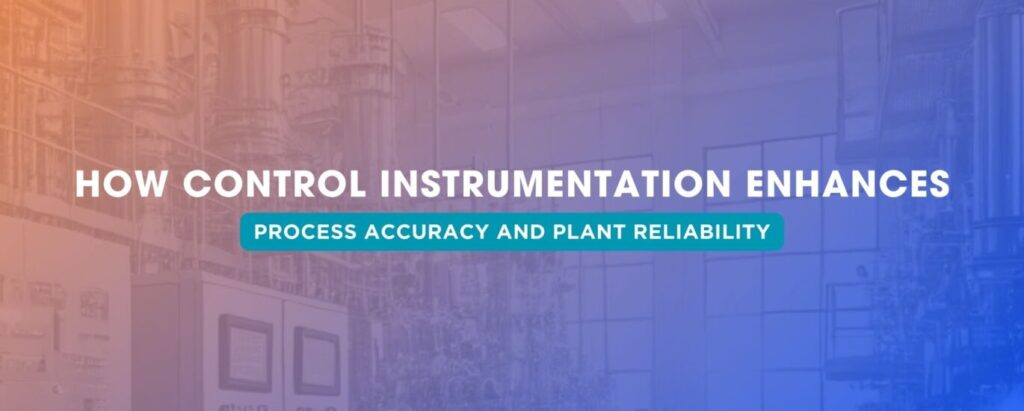
In today’s fast-paced industrial landscape, maintaining accuracy, efficiency, and reliability across complex processes is crucial for sustained success. Whether in oil and gas, pharmaceuticals, power generation, or chemical manufacturing, precision and consistency are non-negotiable. This is where process instrumentation plays a pivotal role. From measuring temperature, pressure, and flow to regulating automated systems, process instrumentation serves as the backbone of process stability and safety.
This blog delves deep into how control instrumentation improves process accuracy and enhances plant reliability, while supporting productivity and compliance in various industrial sectors.
What is Control Instrumentation?
Control instrumentation refers to a set of tools, devices, and systems used to measure, monitor, and control industrial processes. These instruments collect real-time data from processes, enabling operators and automated systems to make informed decisions, maintain process parameters, and ensure optimal operating conditions.
Types of Control Instruments
- Pressure Transmitters and Gauges
- Temperature Sensors and Controllers
- Flow Meters
- Level Transmitters
- Control Valves and Actuators
- Programmable Logic Controllers (PLCs)
- Supervisory Control and Data Acquisition (SCADA) Systems
These devices work in harmony to ensure that the physical variables of a process remain within defined limits.
Importance of Accuracy in Industrial Processes
Accuracy in industrial processes directly impacts product quality, safety, energy consumption, and regulatory compliance. A small error in temperature or pressure measurement can result in defective products, energy wastage, or dangerous conditions.
How Control Instrumentation Ensures Accuracy
- Real-Time Monitoring: Sensors continuously feed data to control systems, allowing for timely corrections.
- Feedback Mechanisms: Closed-loop control systems automatically adjust variables to match desired setpoints.
- High Precision Components: Modern control instruments are built with advanced sensing technologies and robust calibration standards.
Example: In pharmaceutical manufacturing, maintaining exact temperature during a reaction is vital for ensuring drug efficacy. Any deviation could result in product rejection or regulatory issues.
Enhancing Plant Reliability through Control Instrumentation
Reliability refers to the ability of a plant to operate without unplanned downtime or safety incidents. Control instrumentation supports this by identifying anomalies early and enabling predictive maintenance.
Key Benefits:
- Early Fault Detection
- Sensors identify deviations from normal operating conditions.
- Alerts and alarms notify operators of issues before they escalate.
- Minimized Downtime
- Predictive analytics allow for maintenance before failure occurs.
- Automation systems reroute or adjust processes to maintain uptime.
- Consistent Product Quality
- Accurate instrumentation ensures consistent process variables.
- Quality control systems integrate with process instrumentation.
- Improved Safety
- Critical parameters such as pressure and temperature are constantly monitored.
- Emergency shutdown systems (ESD) are linked to control instruments.
Control Instrumentation in Key Industries
1. Oil and Gas
- Application: Pressure transmitters, flow meters, temperature sensors
- Benefits: Prevent pipeline rupture, reduce leaks, ensure safe storage of volatile substances
2. Chemical Manufacturing
- Application: pH sensors, control valves, SCADA
- Benefits: Maintain chemical balance, reduce risk of hazardous reactions
3. Pharmaceutical Industry
- Application: Cleanroom temperature and humidity sensors, batch control systems
- Benefits: Compliance with GMP and FDA standards, improve batch consistency
4. Power Generation
- Application: Turbine temperature sensors, boiler control systems, level sensors
- Benefits: Improve efficiency, prevent overheating, reduce emissions
5. Food and Beverage
- Application: Flow meters, temperature controllers, hygiene-compliant instruments
- Benefits: Maintain food safety, reduce contamination risk, ensure product uniformity
Digitalization and Smart Control Instrumentation
Modern control instrumentation is no longer limited to analog readings or manual adjustments. The rise of Industry 4.0, IIoT (Industrial Internet of Things), and AI/ML integration has transformed traditional control systems into smart, self-learning platforms.
Key Technologies:
- Wireless Instrumentation
- Cloud-Connected Devices
- Edge Computing for Real-Time Analysis
- AI-Based Predictive Maintenance
These technologies enable greater flexibility, reduced wiring costs, remote monitoring, and higher levels of automation.
Example: A smart flow meter not only measures flow rate but also analyzes patterns to predict future blockages or efficiency losses.
Calibration and Maintenance of Control Instruments
Accurate measurement and reliability depend on proper calibration and maintenance. Regular calibration ensures instruments stay within tolerance, while preventative maintenance reduces the likelihood of unexpected failures.
Best Practices:
- Scheduled Calibration Intervals
- Use of Certified Calibration Tools
- Environmental Considerations (e.g., temperature, dust, vibration)
- Record Keeping and Compliance Logs
Regulatory Compliance and Control Instrumentation
Industries such as pharmaceuticals, food processing, and chemicals are bound by stringent compliance requirements (e.g., FDA, ISO, IEC). Control instrumentation helps companies:
- Maintain audit-ready documentation
- Prove product consistency and quality
- Meet safety and environmental standards
Example: A pharmaceutical company must demonstrate that every batch is produced under identical conditions. Control systems log every temperature, pressure, and mixing duration for verification.
Integration with Automation Systems
Control instrumentation is a foundational component of broader automation systems. Instruments feed data to PLCs and SCADA systems, which control actuators and make process decisions.
Benefits of Integration:
- Real-time control and adjustments
- Centralized monitoring across multiple systems
- Remote troubleshooting and diagnostics
- Increased energy efficiency
Case Study: Improving Plant Efficiency with Control Instrumentation
Client: Food processing plant with inconsistent pasteurization quality
Challenge: Manual temperature readings led to variations in product shelf life
Solution: Installed automated temperature sensors with PID controllers
Results:
- Improved product consistency
- Reduced batch rejections by 40%
- Achieved ISO food safety certification
How Our Company Supports Industrial Control Instrumentation
At Japsin Instrumentation, we specialize in providing advanced process instrumentation solutions designed to meet the exact needs of modern industries.
Our Offerings Include:
- High-precision pressure, flow, temperature, and level instruments
- Control systems integration (PLCs, HMIs, SCADA)
- IoT-enabled smart devices for remote monitoring
- Calibration and support services
Industries We Serve:
- Oil & Gas
- Pharma
- Food & Beverage
- Chemicals
- Power & Energy
Why Choose Us:
- Industry-certified products
- Customized solutions for unique process requirements
- Technical expertise and consultation
- After-sales service and training
Future of Control Instrumentation
As manufacturing continues to evolve, control instrumentation will be at the center of innovation. Expect to see:
- Increased AI and ML integration
- Blockchain for process validation
- Fully autonomous production lines
- Sustainable, energy-efficient instrumentation